elcom
Pallet transfer system TLM 2000
The TLM 2000 transfer system is particularly suitable as a standard system for loads with total weight up to 10 kg per pallet (workpiece carrier + product holder + product).
The maximum traction in accumulation mode is 60–150 kg, depending on the configuration (with reference to a transfer unit’s length of 6 m).
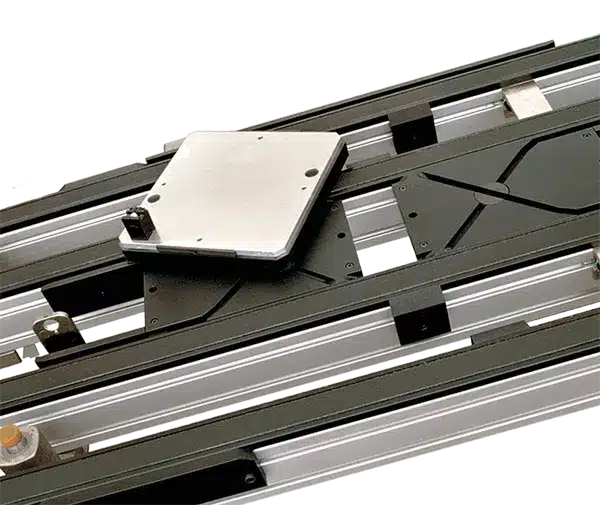
General principle of TLM 2000 transfer
The general principle of the TLM 2000 transfer is based on the movement of the workpiece pallets along a predefined path. This movement is ensured by two parallel notched bands which are located under the pallets. These strips facilitate the installation of stops, indexing and other elements necessary for handling pallets.
The retractable pins play a crucial role in the TLM 2000 transfer. They are located under the pallet and perform several functions. First of all, they ensure the guidance of the pallet using four pins when it moves along straight sections. Then, when passing through turns and diversions, two of the pins retract while the other two remain in contact with specific cams to guide the pallet precisely.
The use of retractable pins allows smooth and precise handling of the pallets in the curved areas of the TLM 2000 transfer. The non-retracted pins ensure safe and stable guidance, while the retracted pins allow the pallet to follow turns and diversions without issue.
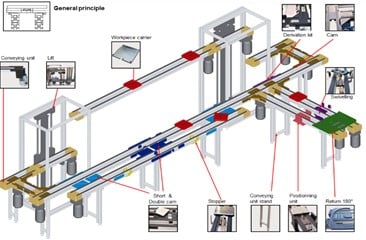
What pallets are used in the TLM 2000 transfer?
The pallets used in the TLM 2000 transfer have a standard size of 200 x 200 mm up to 400 x 400 mm. They are designed to support the parts to be transported and are equipped with a patented elcom system. This system includes retractable pins, guides and branch kits.
Dimensions of the TLM 2000 transfer
The transport units used in the TLM 2000 transfer have a standard maximum length of 6250 mm. For the TLM 2000 model with a toothed belt and a light motor, the standard maximum length is 6160 mm. If larger dimensions are necessary, it is possible to combine several elements by placing them end to end.
If large accumulations of pallets are expected, the length of the transport units can be adapted according to the load. It is important to take this consideration into account to ensure optimal operation of the system.
To control pallet accumulations, it is recommended to position detectors along the transfer path. These detectors make it possible to monitor and regulate the flow of pallets, thus avoiding congestion or blockages.
Equipping all cylinders with flow regulators is imperative in the TLM 2000 transfer. These flow regulators make it possible to control the speed of movement of the pallets and ensure precise and safe handling.
In the case of long lengths of transport units, it is possible to make cuts to facilitate the dismantling of machines or to allow access to certain specific areas. These cuts can be made conveniently while maintaining the integrity and functionality of the transfer system.
The role of pallets
The pallets used in the TLM 2000 transfer play an essential role in allowing the attachment of the supports, which ensures precise positioning of the assembly during the transfer process.
Each pallet is made up of two plates: an aluminum upper plate and a PA (polyamide) base with a very low coefficient of friction and high wear resistance. The upper aluminum plate is used to fix the workpiece holders and guarantees the geometric stability of the pallet as well as the precision of the positioning. Depending on customer needs, machining such as drilling and tapping can be carried out on the plate. To ensure wear resistance and optimal precision, treated steel barrels are positioned in the aluminum plate.
The PA base rests on the conveyor belts and houses the 4 guide pins specific to elcom. These guide pins allow the pallet to move correctly along the transfer system. In addition, the base is designed with a specific shape to ensure the proper functioning of the stops. Metal bars are also present on each side of the pallet, allowing detection of pallets at different stations in the system.
Standard pallets are available to accommodate the parts to be transported, but in some cases the surface area of the standard pallet may not be sufficient. In such cases, special pallets can be supplied to meet specific requirements. By using the 4 guide pins present on the pallets, it is possible to vary the length of the pallets, which makes it possible to optimize the system cycle times.
The guide pins remain in the position corresponding to the nearest standard pallet, meaning that all standard elements such as cams can be used without modification. This flexibility in pallet length opens up different possibilities and variants for the TLM 2000 transfer, depending on the specific needs of each application.
Examples of variable dimensions of Elcom pallets:
The arrangement of the guide pins is identical in width.
However, lengthwise the guide pins of a 400×400 pallet have a greater gap than the 200×200 pallets. If pallets of different dimensions are used on the same transfer line, the arrangement of the guide pins must be identical.
Adapt the pallets
The TLM 2000 transfer pallets can be specifically tailored to meet customer needs. Although standard pallets are available for installing parts, it is often the case that the surface area of the standard pallet is not sufficient for certain applications.
In such cases, special pallets must be provided. These special pallets are generally defined by the customer and are applied to existing standard pallets. This allows specific adaptations to be created to meet the particular requirements of each client.
Standard pallets as well as specific adaptations form the basis for safe material transport in the TLM 2000 transfer. By optimizing the characteristics of the pallets, it is possible to make them optimally available to the workstations, thus ensuring a smooth and efficient transfer process.
In addition to precise positioning of parts, pallets also play a role in dissipating pressure forces. The standard modules of the TLM 2000 transfer are designed to allow non-deformable diversion of pressure forces up to 40 kN (4 tonnes). This ensures safe and stable handling of parts during the transfer process.
TLM 2000 CONVEYING UNITS
TLM 2000 conveying units are essential components in industrial pallet movement and accumulation systems. They offer efficient solutions for transferring loads in production and logistics facilities. The TLM 2000 transport units are available in different variants depending on the specific needs of the application.
TRANSFER UNIT WITH FLAT BELT
In this belt line variant, the required flat belt for product transport is moved via a pulley driven by a chain of motor/transmission combinations located underneath it.
In the standard variant, the drives can only be attached to the pulley’s heads.
DIRECT CONVEYING UNITS
With a direct drive, the conveyor belt is divert over various rollers in such a way that it loops around the drive shaft, to which the motor/drive combination is directly flange-mounted. In the standard variant, the drives can only be attached to the pulley’s heads. The direct drive gives you a maintenance-free transfer system unit. The belts lines with direct drives can be used with flexproof connected drive belts (see Transfer technology for details).
LIGHT CONVEYING UNITS
This variant for the TLM 2000 implements transport of workpiece carriers with timing belts. The use of 25 mm wide anti-static timing belts enables to increase the transported load compared to flat belts and simultaneously simplifies maintenance work, since the transfer system’s belts can be replaced quickly. In the standard variant, the drives can only be attached to the pulley’s heads.
HEAVY CONVEYING UNITS TIMING BELT
This variant for the TLM 2000 implements transport of workpiece carriers with timing belts. The use of 32 mm wide anti-static timing belts enables to increase the transported load compared to the lighter timing belt variants and simultaneously simplifies maintenance work, since the transfer system’s belts can be replaced quickly. In the standard variant, the drives can only be attached to the pulley’s heads.
In summary, TLM 2000 transport units offer a complete range of solutions for the movement, accumulation and transport of pallets in industrial environments. Their mounting flexibility, compatibility with other drive units and ease of maintenance make them essential components for optimizing logistics and production operations.
TLM 2000 COMPONENTS
The TLM 2000 transfer system is made up of several components and modules that manage the movement and positioning of pallets. Here is a detailed description of each component:
STOPPER
Stoppers are used to stop or isolate the workpiece carriers. Various types of stoppers can be selected depending on the properties of the workpiece (weight, transport speed, damping requirement, etc.).
In order to carry out controlled processing on a production line, it must be possible to pick the workpieces on the workpiece carriers from the correct position. For this purpose, the workpiece carrier is held in place by the stopper integrated into the positioning unit until the complete workpiece carrier is lifted out into the C rails by a pneumatic cylinder and there is no further contact with the transport medium.
POSITIONING UNITS
Cam TLM 2000
The cams (types ED, EG, SD and SG) enable to change the direction of the workpiece carriers between two transfer units at a 90° angle.
The workpiece carriers are driven by two inner pins while the two outer pins are retracted.
The derivation is used with a cam in order to give the workpiece carrier a specified direction by retracting the pins. The two cylinders are controlled by a single solenoid-valve.
Derivation
Return 180°
The return 180° allows to turn workpieces around in very confined spaces, e.g. in small cycles or cycle time independent workstations.
Rotation of the workpiece carriers by 90° by latching and retracting the pins. To rotate by 180°, it is possible to arrange two 90° rotation devices one after another.
SWIVELLING 90°
SHORT CAM
The short cam and the crossings allow to divert the workpiece carriers from a main transport line to a secondary transport line without additional motorisation.
Double cams are similar to short cams and also allow pallets to be diverted from a main line to a secondary line without additional motorization. They offer the same advantages in terms of economy, reduced bulk and ease of management.
Double cams
CONVEYING UNIT STAND
Support to fit conveying units on table or frame.
Elevators allow the return of pallets from below or above a line, or the distribution of pallets over several levels. Each elevator is built from standard elements and is adapted according to the dimensions of the pallets, the necessary strokes and other parameters specific to the transfer line.
Elevators
These different components and modules of the TLM 2000 transfer system offer varied functionalities to manage the movement and positioning of pallets according to the specific needs of a production or transfer line.
Video of transfer TLM 2000
One question ?
Our experts are here to answer your questions, support you, and guide you through all your projects.