elcom
Pallet transfer system TLM 5000
The pallet transfer systemTLM 5000 is ideal for assembly of large products from 500×500 mm to 1000x100mm in ESD or cleaning room environements . It has been designed with a specific inflatable technology.
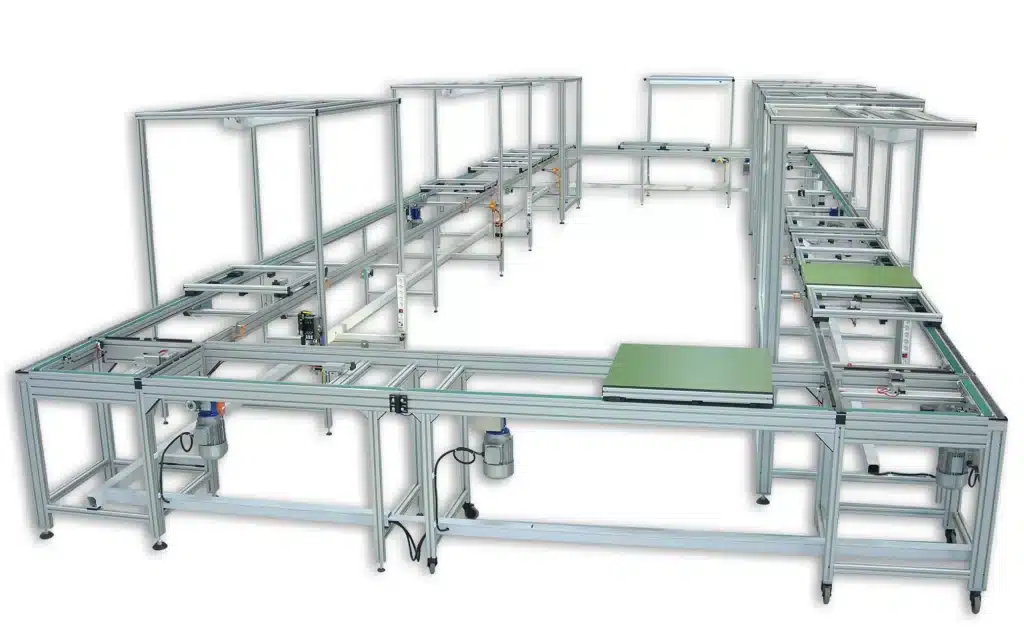
Presentation of the Modular Linear Transfer 5000
The TLM 5000 is an industrial system developed by elcom, leader in the field of conveying solutions designed for the movement of bulky part-carrying pallets, this system offers exceptional modularity and adaptability. Pallets with dimensions ranging from 500×500 to 1000×1000 can be easily moved with great precision and efficiency
These pallets can be made from different materials and are equipped with multi-directional rollers to make them easier to move. They run on stainless steel treads designed to support significant loads.
Pallet movement is ensured by pneumatically pressure-controlled belt drive units. It is also possible to configure sections without drive, allowing manual movement of the pallets if necessary.
The TLM 5000 elcom integrates a pneumatic management device in each corner, which allows the pallet to cushion itself and change direction automatically, without requiring an additional controller.
The modular architecture of the TLM 5000 elcom offers the possibility of optimizing the dimensions of the pallets according to the products transported. Additionally, subsequent expansions or modifications can be easily made, providing increased flexibility and adaptability to the system.
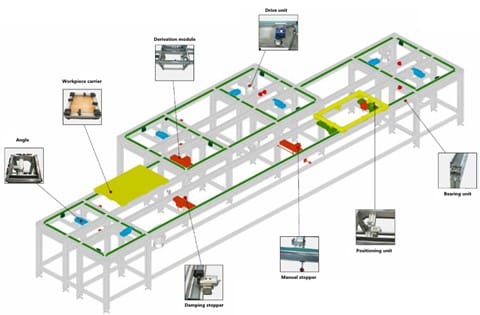
Advantages of the TLM 5000
- Modularity and flexibility: The TLM 5000 stands out for its modular design, which makes it easy to adapt to the specific needs of each company. Modules can be assembled in different configurations, allowing optimal flexibility to accommodate various space and process constraints.
- Saving time and money: By optimizing the movements of large workpiece pallets, the TLM 5000 helps reduce downtime and increase overall productivity. Labor costs are also reduced through the automation of material handling tasks, resulting in a significant improvement in operational efficiency.
- Precision and reliability: Thanks to its advanced control system, the TLM 5000 ensures precise positioning of workpiece pallets. This ensures gentle handling and reduces the risk of product damage or loss. System reliability also helps minimize human errors and unexpected interruptions to the production process.
- Reinforced security: elcom places great importance on the safety of operators and equipment. The TLM 5000 has built-in safety features such as obstacle detection sensors and advanced monitoring systems. This helps prevent potential accidents and ensures a safe working environment.
TLM 5000 pallets
TLM 5000 pallets are modularly designed, allowing different pallet configurations to be created. The multidirectional rollers integrated into PA corner kits, positioned under the four corners of the pallet, ensure its rolling.
Each corner block is equipped with a shock absorber pad to reduce shock and noise when accumulating several pallets, a multidirectional roller and a detection plate for pallet management.
The pallet drive is provided by the corner blocks and central blocks, the number of which varies depending on the size of the pallet. The central blocks allow the pallets to be quickly started in the corners and stopped on the stops.
Precise positioning on the indexers is achieved using two centering bushes.
Various combinations can be used to create the pallet top depending on the load, workpiece carrier position and dimensions. This may include the use of 40×40 aluminum profiles or other materials such as aluminum plates of different thicknesses (8, 10, 12 or 16 mm), steel plates, beech plywood plates or compact laminate boards.
The TLM 5000 transport unit
The transport unit of the TLM 5000 consists of two separate elements: the bearing part and the drive part.
The bearing part can have a maximum length of 6 meters. The rollers located under the pallet roll on a stainless steel strap, which allows effortless movement and ensures a long lifespan. The load of the pallet is supported by a profile measuring 80×40 topped by a strap support profile, which gives great rigidity to the whole.
The drive part can also reach a maximum length of 6 meters. The movement of the pallet is ensured by the inflatable unit. A toothed belt, which rotates constantly, is supported by a sliding profile made of technical plastic. Under this profile is a pneumatic membrane which exerts a vertical force. Adjusting the air pressure in the membrane makes it possible to vary the thrust force exerted on the pallet.
To optimize the number of motors used, it is recommended to use the same drive unit in the corners of the system. This approach allows better management of the propulsion effort.
In many Lean-oriented applications, only the rolling part is used, while the pallets are transferred manually from one station to another. This configuration allows for increased flexibility and adaptation to the specific needs of each process.
TLM 5000 components and modules
Positioning units allow to stop and position the workpiece
carriers at an assembly workstation for the purpose of performing precision work. The workpiece carrier is first stopped by a damped stopper and then positioned with a pin locating system. No vertical movement of the workpiece carrier occurs. It is possible to add an anti bouncing back device.
Angles
The angle modules make it possible to change the direction of workpiece carriers by 90° around the angles of the transfer system. The angle is self-supporting and is supplied with 4 rigid feet and 2 inflatable unit set and controlled with a pneumatic shock absorber. The shock absorber goes back into position during the transfer movement to hold the next workpiece carrier that arrives in a damped manner. Accumulation mode at the angle is not possible.
STOPPER
The stoppers ensure that the workpiece carriers can be stopped for the upcoming production processes.
The use of a positioning unit may be necessary depending on the precision requirements of the production process.
The manually controlled stopper does not require management. However, the workpiece carrier should not exceed a maximum weight of 30 kg. An anti bouncing device is integrated into the stopper.
PNEUMATIC STOPPERS
Pneumatic stoppers are used at manual work stations or to control backlogs. They make it possible to stop the workpiece carriers at the front edge or below the pallet in the rear area (with respect to the direction of motion). An adjustable pneumatic shock absorber is integrated, which stops the pallets with cushioning. When then stopper changes direction, the shock absorber automatically returns to operational readiness.
Breakout modules
Branch modules allow you to create secondary transfer lines. They offer the possibility of choosing the direction of the pallets, thus facilitating routing and transfer in different lanes.
DRIVING UNIT
Branch modules allow you to create secondary transfer lines. They offer the possibility of choosing the direction of the pallets, thus facilitating routing and transfer in different lanes.
Transfer 5000
One question ?
Our experts are here to answer your questions, support you, and guide you through all your projects.