Elcom
Conveyor systems
Conveyors are essentially used for the continuous management of the flow of goods or products.
The choice of the conveyor belt depends on the application but also the field of activity.
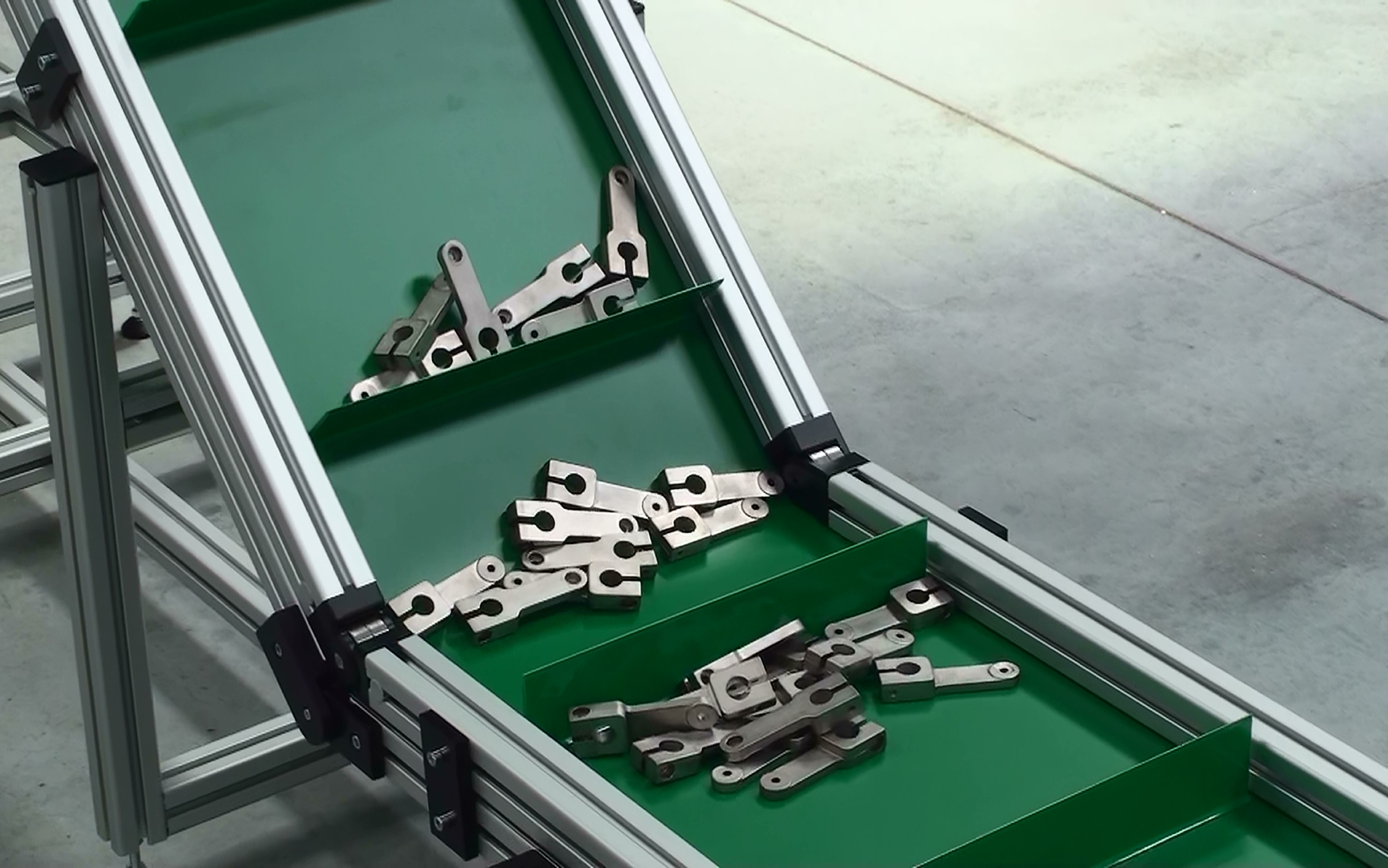
CONVEYOR C20
CONVEYOR C80
CONVEYOR TB24
CONVEYOR TB50
CONVEYOR TB90
Inflatable belt conveyor
Roller conveyor
Belt Conveyor
Our standard flat belt conveyors are a classic in a majority of conveyor technology applications. Individual workpieces and packaging units, and in many cases also bulk goods, are transported via a conveyor belt stretched over a frame using pulleys. We cover standard segment belt widths from 20 to 1000 mm and axle distances from 300 to 6000 mm.
With elcom , the belt conveyors are divided into 4 classes according to the diameter of the pulleys on the belt heads; these are the elcom Ø20, Ø40, Ø80 and Ø90 series belt conveyors. All systems use flat belts as the conveyor belts; the belt type is adapted to your requirements.
CONVEYOR C20 : Compact conveyor on a 20 mm profile 5 base, for very small, lightweight parts.
CONVEYOR C40 : Compact conveyor on a 40 mm profile 8 base, for all types of part
CONVEYOR C80 : Compact conveyor manufactured from h’elcom‘s profile range, dedicated to the conveying of light and bulky loads.
CONVEYOR C90 : Conveyor for heavier, high-volume components.
Elcom has experts who help you in the design of your project, they are technicians, like you!
Eco-friendly toothed belt conveyors
Conversely, notched belt conveyors are used for heavy parts or for stricter positioning requirements. They are often used with multiple conveyor lines for a synchronicity requirement. Unlike belt conveyors, recovery of specific parts can easily be implemented. Notched belt conveyors are most of the time dedicated to providing parts for robotic cells or for gantry robots.
Elcom notched belt conveyors are divided into 2 ranges depending on the diameter of the end pulleys: 40 and 90 notched belt conveyors. All systems are equipped with notched belts. The type of tape is suitable for your needs.
CONVEYOR 40: Compact conveyor made from base 8 profiles, width 40 mm for all types of parts.
CONVEYOR 90: Conveyor made from base 8 profiles, width 90 mm for heavy parts of large volume.
In summary, the h’8 40 profiles adapt perfectly to equivalent profiles of the same section already present in your workshops. However, by opting for h’8 40, you benefit from the possibility of integrating the transformation directly into the heart of your workshops, making them perfectly modular and scalable.
h’8 40 profiles can find applications in many other industrial sectors depending on the specific needs of each project.
By choosing h’8 40, you benefit from the efficient supply chain by a global partner with an extensive presence in France, and Europe. In addition, you can count on the expert support of the H’8 40 team and be assured of robust, durable and technically certified solutions.
Video of belt conveyor
TB range conveyors
The TB (Belt Conveyor) range is a line of belt conveyors offered by Elcom. TB Series conveyors are designed to meet a variety of industrial material transportation needs.
The conveyors in the TB range are distinguished by their modular structure and their versatility. They can be configured in different ways to suit the specific requirements of each application.
Types of conveyors:
Straight conveyors allow linear movement of products over a given distance.
Curved conveyors are designed for applications where it is necessary to change the direction of material transport.
Z-shaped conveyors allow Z-shaped paths to be made to optimize the available space.
Bandwidth :
The conveyors in the TB range are available in different belt widths to adapt to the dimensions of the products to be transported. Elcom offers standard width options, but can also supply custom conveyors to meet specific customer needs.
Modular structure: TB conveyors are built on a modular extruded aluminum structure, which makes them both light and robust. This modular design facilitates the assembly, modification and maintenance of conveyors, providing great flexibility of use.
Belt Options: Elcom offers different belt options for TB conveyors, depending on the needs of the application. This includes PVC, polyurethane or rubber belts, offering different characteristics of wear resistance, adhesion and compatibility with the products being transported.
Accessories and features: TB range conveyors can be equipped with various accessories and features depending on the specific needs of each application. This may include side guides, belt centering devices, inspection hatches, proximity sensors, sorting systems, etc.
The different types of conveyors
There are different types of conveyors with their own technical specifications.
Flat belt conveyors
Flat belt conveyors:
Flat belt conveyors are industrial equipment used for the transportation and handling of various bulk or packaged materials in many industrial sectors. These conveyors consist of a rubber, PVC or polyurethane conveyor belt, stretched between two pulleys to form a continuous loop. The surface of the belt is flat and smooth, allowing smooth movement of the transported products.
Use of flat belt conveyors:
Flat belt conveyors are widely used in various industries for efficient and safe transportation of different types of loads. In the mining industry, these conveyors are essential for the extraction and handling process of mining materials such as coal, iron ore and copper. In the food industry, they facilitate the movement of food products such as grains, vegetables, fruits and dairy products, respecting hygiene and food safety standards.
Flat belt conveyors are a lighter and quieter alternative to chain conveyors, available in aluminum or stainless steel. They are used in all types of fields:
Agri-food
Pharmaceutical
Cosmetic
Etc…
Manufacturing of flat belt conveyors:
Flat belt conveyors are manufactured using high quality materials and advanced technologies. The conveyor belt is designed to withstand specific loads and environmental conditions. Conveyors are generally equipped with tensioning and guiding systems to keep the belt in an optimal position and ensure stable operation. Dimensions, length and width of smooth belt conveyors can vary depending on specific industry and application needs.
Advantages and features of flat belt conveyors:
Flat belt conveyors offer several advantages, such as efficient transportation of bulk or bundled materials, reduction in labor required for handling operations, possibility of automation for better productivity, design flexibility to accommodate different working environments, and reduced risk of product damage through smooth, controlled movement.
Timing belt conveyors are also industrial equipment used for transporting and handling materials in different industrial applications. These conveyors are equipped with a conveyor belt equipped with notches or teeth which mesh with sprockets, thus allowing positive movement and better adhesion of the transported products.
Use of toothed belt conveyors:
Timing belt conveyors are used in industries such as the automotive industry, the pharmaceutical industry and the packaging industry. In the automotive industry, these conveyors are essential for transporting parts, components and assembled vehicles along the production line. In the pharmaceutical industry, they are used for the precise transport of medicines, packaging and vials. In the packaging industry, toothed belt conveyors facilitate the movement of packaged products such as boxes, cartons and pallets.
Timing belt conveyors
Manufacturing of toothed belt conveyors:
Timing belt conveyors are manufactured using sturdy, durable materials and specially designed gear and notch systems. The notched conveyor belt is configured to precisely mesh with the sprockets, ensuring positive and smooth movement of the products being transported. As with smooth belt conveyors, the dimensions and characteristics of toothed belt conveyors can be adapted to the specific needs of each industry.
Advantages and functionalities of timing belt conveyors:
Timing belt conveyors offer several advantages, including positive and smooth movement of the products being transported, increased grip through notches or teeth, ability to transport heavier loads and inclined products, and high reliability for transport and handling operations. These conveyors are often used in environments where precise power transmission is required, enabling efficient transportation of products across different industrial sectors.
Roller conveyors
Roller conveyors are material handling systems used to transport loads from one point to another in various industries, such as logistics, distribution and manufacturing. They are designed to facilitate the efficient movement of objects on a series of motorized or gravity rollers.
Roller conveyors generally consist of a solid support structure to which lengthwise aligned rollers are attached. The rollers can be made of steel, plastic or aluminum, depending on the specific requirements of the load to be transported. They are spaced to create a continuous surface on which objects can roll smoothly.
These conveyors can be powered by electric motors, compressed air motors or operate in a gravity manner by exploiting the natural slope of the system. Electric motors are typically used for motorized roller conveyors, providing precise speed and stopping control.
The advantages of roller conveyors are numerous. They enable efficient transport of heavy or bulky loads over long distances. Rotating rollers reduce friction, making it easier to move objects. Additionally, roller conveyors can be designed for specific applications, such as sorting, accumulation, load transfer from one level to another, etc.
These conveyor systems also offer flexibility in terms of configuration and networking. They can be integrated into existing installations, modified or expanded according to business needs. Roller conveyors can be used alone or in combination with other types of conveyors to create a more complex material handling system.
Regarding safety, roller conveyors can be equipped with protective devices such as protective covers, safety barriers and emergency stop systems to ensure the safety of operators and prevent accidents.
The different types of roller conveyors
Free roller conveyor:
This type of roller conveyor operates on a gravity basis, exploiting the natural slope of the system to move loads forward. The rollers are arranged to allow objects to roll freely without external power. They are often used for transporting light loads over short distances.
Motorized roller conveyor:
Unlike the free roller conveyor, this type of conveyor is equipped with motorized rollers that propel loads along the system. Electric motors provide the power needed to move objects with precision and control. These conveyors are commonly used for transporting heavier loads over longer distances.
Curved free roller conveyor:
This type of free roller conveyor is specifically designed for transporting loads around turns or curves. The rollers are arranged to create a continuous curve, allowing objects to follow the desired path by exploiting gravity. This makes it easier to move loads around corners without requiring external power.
Curved motorized roller conveyor:
Similar to the motorized roller conveyor, this type of conveyor has motorized rollers that help propel the loads along the curve. Electric motors provide the power needed to move objects in a controlled manner around turns or curves. These conveyors are used when heavier loads or precise speed control are required when transporting around curves.
How to choose the right type of conveyor?
You have to collect 5 information :
-product size, weight, typology(liquid, solid…)
-production rate (conveyor speed)
-environmental conditions : wet, cleanroom, oily, water…
-incline/decline sections
-Specific requirements : accumulation, sorting…
Conveyors for industries
In modern industry, conveyors play a vital role in optimizing production processes and ensuring maximum efficiency. These automated transport systems allow components to be handled and moved throughout the production line quickly, precisely and reliably.
Conveyors used in industry are specially designed to meet productivity, quality and safety requirements. They must be capable of transporting heavy loads, often of various shapes, while maintaining a high production rate. These conveyors are also designed to withstand harsh environments, such as extreme temperatures, wet or corrosive working conditions.
Among the different types of conveyors used in the industry, we find belt conveyors, chain conveyors, roller conveyors and curved conveyors. Each type of conveyor offers specific advantages depending on the needs of the production line.
Belt conveyors are frequently used to transport parts of different sizes and shapes. They offer great flexibility and can be adapted to specific configurations thanks to options such as side guides or cleats. Chain conveyors, on the other hand, are often used to transport heavy and bulky loads, offering great strength and high load capacity.
Roller conveyors are particularly suitable for moving parts or containers along a production line. They enable smooth transfer of loads and can be equipped with speed control systems to adjust the production rate. Curved conveyors, finally, are used for transporting parts in curved or angular directions, providing great stability and good grip.
Besides transporting parts, conveyors in industry can also be used for other applications, such as sorting, inspection or packaging of finished products. These automated systems help speed up production processes, reduce errors, and improve overall product quality.
Conveyors can be motorized or not depending on the specific needs and expectations of the industry.
Custom industrial conveyors
We have a large number of different conveyors available in many different variations. However, if these models don’t meet your requirements, we can produce a customized conveyor in aluminum or stainless steel profile.
We can meet all your requirements with chain conveyors, rollers, modular belts, pallets, etc. Our different conveyor ranges ensure constant adaptability.
From simple transport of standard products, to more specific solutions such as accumulation tables, to the conveying of difficult products (e.g. grains of rice), our solutions are diverse and can respond to a multitude of problems.
Examples of tailor-made conveyors
There are different tailor-made conveyors
Passageway conveyors:
Telescopic passageway conveyors are industrial transportation systems specially designed to allow the safe passage of operators or personnel over or through the conveyor. They are used in industrial environments where it is necessary to have direct access for maintenance, inspection or human intervention operations. These conveyors are usually equipped with hatches, doors or other mechanisms to create unobstructed access when necessary. They guarantee the safety of operators by avoiding any risk of accident or injury when they interact with the conveyor system.Pinch conveyors
Pinch conveyors are designed for vertical transportation of objects, and built-in manways allow operators to move safely from one level to another within a facility. They are often used in warehouses, distribution centers, production facilities and logistics industries to facilitate the vertical movement of goods and operators.
H’Factory has already designed numerous specific conveyors based on pinch systems.